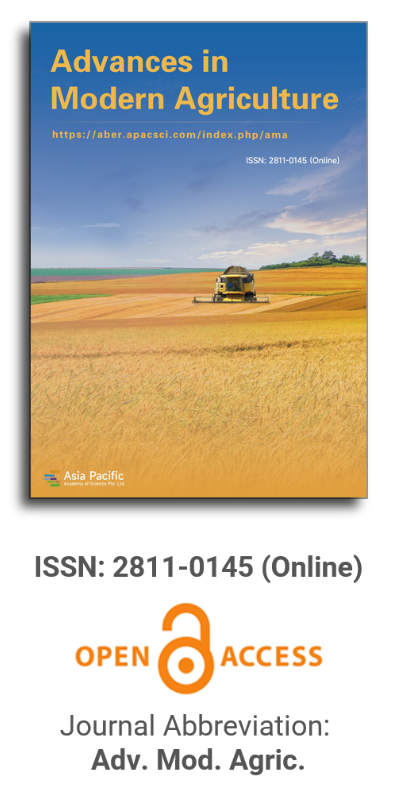
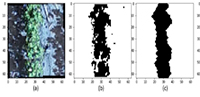
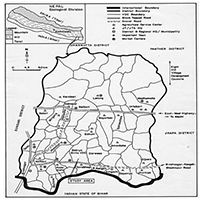
Gradient throwing characteristics of oscillating slat shovel for rhizome crop harvesters
Vol 3, Issue 1, 2022
VIEWS - 3909 (Abstract)
Download PDF
Abstract
An oscillating slat shovel has presented a promising application potential in the energy-saving and efficient harvesting of deep rhizome crops. This new type of shovel slat integrated harvesting device was developed using gradient amplitude and gradient vibration technology. This study aims to clarify the working characteristics of oscillating slat shovels and the mechanism of throwing separation. The throwing coefficient was selected to characterize the throwing separation ability of the slat shovel work plane. A motion analysis was made to calculate the swing acceleration of the slat shovel work plane. An analytical equation of the throwing coefficient was then established to combine with the working process, the periodic variation of the throwing coefficient, and the influence of parameters, including the amplitude, vibration frequency, and working length. The results showed that the throwing coefficient gradually increased at each point of the slat shovel work plane, indicating outstanding gradient throwing characteristics and strong throwing ability. The maximum throwing coefficient was 9.98–19.72 in the separation area. After that, an investigation was made to determine the influence of the structure and working parameters of the oscillating slat shovel on the soil-throwing separation performance. The EDEM-MBD coupling simulation model of the single pendulum shovel gate was established to simplify the structural model and the interaction between the rhizome, soil, and working components, where the indicators were set as the traction resistance, driving torque, the maximum separation distance between the soil and the slat (separation distance), and the ratio of the separated soil quality of each functional area of the work-plane to the total soil mass (separation ratio). A single-factor test was carried out with the amplitude, vibration frequency, and forward speed as factors. The results indicated that: 1) There were outstanding strong-weak cycles in the traction resistance and driving torque due to the gradient throwing characteristics of the oscillating slat shovel, soil viscosity, and plasticity. In the strong period, there was a large interaction force between the shovel slat and soil, where the maximum separation distance occurred at the middle point of the separation area at the endpoint of the cutting stroke. 2) The amplitude was negatively correlated to the traction resistance but positively correlated with the driving torque and separation distance. The vibration frequency was negatively correlated to the traction resistance, driving torque, and separation spacing. The forward velocity was positively correlated to traction resistance and driving torque but negatively correlated to the separation distance. 3) There was a small influence of amplitude and vibration frequency on the separation ratio. There was a low separation of oscillating slat shovels with the increase in forward velocity. 4) A combination of parameters was achieved when the amplitude was 7–11 mm in the strong period, where the average traction resistance was about 1580.93–2019.9 N, the maximum driving torque was about 224.04–322.11 N·m, and the maximum separation distance was about 59.58–98.3 mm. 5) The average traction resistance was about 1416.43–1866.38 N, the maximum driving torque was about 315.28–364.19 N·m, and the maximum separation distance was about 78.43–94.67 mm when the vibration frequency was 6.67–10.67 Hz. 6) The average traction resistance was about 1429.43–2110.48 N, the maximum driving torque was about 241.27–387.78 N·m, and the maximum separation distance was about 62.5–102.5 mm when the forward speed was 0.2–0.4 m/s. An optimal combination of parameters was selected for the field experiment: the amplitude was 9 mm, the vibration frequency was 9.4 Hz, and the working speed was 0.32 m/s. The licorice harvesting test indicated that the traction resistance was about 32.17 kN, the driving torque was about 802.02 N·m, the excavation depth was about 468 mm, and the cleaning rate was about 96.42%. Consequently, the oscillating slat shovel harvesting device can be feasible for smooth and orderly operation as well as the higher separation performance of rhizome-soil, where all the operation indexes meet the national standards. This finding can provide a new method and design reference for the energy-saving and efficient harvesting of rhizomes, especially deep rhizome crops.
Keywords
References
- Yang R, Yang H, Shang S, et al. Design and test of vertical annular separation and conveying device for potato combine harvester (Chinese). Transactions of the Chinese Society of Agricultural Engineering 2018, 34(3): 10–18.
- Zhao Q. Research status and development prospect of potato harvesting machinery at home and abroad (Chinese). Agricultural Engineering 2020, 10(6): 7–10.
- Yang R, Wang Z, Shang S, et al. Design and test of rice bale coating device for peanut joint harvest silage machine (Chinese). Transactions of the Chinese Society for Agricultural Machinery 2020, 51(8): 109–117.
- Luo Q, Ning H, Liu Y, He M. Analysis and evaluation of the current status of rooibos and licorice resources in Xinjiang (Chinese). Protection Forest Science and Technology 2019; 5: 13–16.
- You Z, Hu Z, Wu H, et al. The design and test of 1MCDS–100 A shovel sieve residual film reclaimer (Chinese). Transactions of the Chinese Society of Agricultural Engineering 2017; 33(9): 10–18.
- Zhang R, Sun W, Wu J, et al. The design and research of shovel-screen excitation potato excavator (Chinese). Research of Agricultural Modernization 2015; 36(5): 916–920.
- Zhang Z, Wang Y, Li H, et al. Design and test of hydraulic control crawler self-propelled greenhouse panax notoginseng harvester (Chinese). Transactions of the Chinese Society for Agricultural Machinery 2021; 52(6): 127–135, 158.
- Wei Z, Li H, Su G, et al. The research and development of buffer sieve potato harvester (Chinese). Transactions of the Chinese Society of Agricultural Engineering 2019; 35(8): 1–11.
- Zhang Y, Ou Z, Cui Z, et al. Design and experimental analysis of double roller combined pineapple leaf crushing and returning machine (Chinese). Journal of Agricultural Science and Technology 2017; 19(7): 78–86.
- Yang F, Yang Y, Li W, et al. Design and test of vibration excavation crushing device for hanging yam harvester (Chinese). Transactions of the Chinese Society for Agricultural Machinery 2020; 51(6): 104–111.
- Kim YS, Siddique AA, Kim WS, et al. DEM simulation for draft force prediction of moldboard plow according to the tillage depth in cohesive soil. Computers and Electronics in Agriculture 2021; 189: 106368. doi: 10.1016/j.compag.2021.106368
- Deng G, Huang Y, Zheng S, et al. Improved design and test of vibration chain cassava harvester (Chinese). Modern Agricultural Equipment 2018; 3: 35–39.
- Lipiec J, Czyż EA, Dexter AR, et al. Effects of soil deformation on clay dispersion in loess soil. Soil and Tillage Research 2018; 184: 203–206. doi: 10.1016/j.still.2018.08.005
- Yang R, Yang H, Shang S, et al. The design and test of roller push potato harvester (Chinese). Transactions of the Chinese Society for Agricultural Machinery 2016; 47(7): 119–126.
- Hou J, Chen Y, Li Y, et al. Development of quantitative self-propelled onion combine harvester (Chinese). Transactions of the Chinese Society of Agricultural Engineering 2020; 36(7): 22–33.
- Yang Y, Liao Y, Wang T, et al. Design of self-propelled cassava harvester (Chinese). Journal of Agricultural Mechanization Research 2016; 38(4): 99–102+106.
- Lyu J, Sun H, Dui H, et al. Improved design and test of separation and transportation device for potato excavators in sticky soil (Chinese). Transactions of the Chinese Society for Agricultural Machinery 2017; 48(11): 146–155.
- Xie S, Wang C, Deng W, et al. Mechanism analysis and parameter optimization test of swing separation sieve potato soil separation (Chinese). Transactions of the Chinese Society for Agricultural Machinery 2017; 48(11): 156–164.
- Wei Z, Su G, Li X, et al. Optimization and test of wave screen surface parameters of potato harvester based on discrete element (Chinese). Transactions of the Chinese Society for Agricultural Machinery 2020; 51(10): 109–122.
- Zhang Chao. Design and Experimental Study of Vibrating Grid Licorice Harvester for Combined Excavation (Chinese) [Master’s thesis]. China Agricultural University; 2021.
- Sun Y, Dong X, Song J, et al. Operation parameters optimization of vibration subsoiling test bench (Chinese). Transactions of the Chinese Society of Agricultural Engineering 2016; 32(24): 43–49.
- Dong X, Song J, Wang J, et al. The motion characteristics analysis and vibration frequency optimization of grassland vibration subsoiler (Chinese). Transactions of the Chinese Society of Agricultural Engineering 2012; 28(12): 44–49.
- Sun Y, Dong X, Song J, et al. The self-balancing performance and simulation analysis of multiple vibration subsoilers of vibration subsoilers (Chinese). Transactions of the Chinese Society of Agricultural Engineering 2018; 34(4): 92–99.
- Liu W, He J, Li H, et al. Design and test of double side deep fertilization device for potato micro potato planting machine (Chinese). Transactions of the Chinese Society for Agricultural Machinery 2020; 51(1): 56–65.
- Zhao S, Liu H, Hou L, et al. Development of no-tillage and deep-fertilization sectional corn sowing trencher based on discrete element method (Chinese). Transactions of the Chinese Society of Agricultural Engineering 2021; 37(13): 1–10.
- Yu W, Yang R, Shang S, et al. The design and test of shovel-screen combined peanut segmental harvester (Chinese). Journal of Agricultural Mechanization Research 2016; 38(6): 163–166+171.
- Cheng C, Fu J, Chen Z, Reng L. Vibration parameters of the vibrating screen of the harvester affect the adhesion characteristics of different humidity extracts (Chinese). Transactions of the Chinese Society of Agricultural Engineering 2019; 35(8): 29–36.
- Thakur SC, Morrissey JP, Sun J, et al. Micromechanical analysis of cohesive granular materials using the discrete element method with an adhesive elasto-plastic contact model. Granular Matter 2014; 16(3): 383–400. doi: 10.1007/s10035-014-0506-4
- Xie F, Wu Z, Wang X, et al. The calibration of soil discrete element parameters based on unconfined compressive strength test (Chinese). Transactions of the Chinese Society of Agricultural Engineering 2020; 36(13): 39–47.
- Zhang R, Han D, Ji Q, et al. Study on calibration method of sandy soil parameters in discrete element simulation (Chinese). Transactions of the Chinese Society for Agricultural Machinery 2017; 48(3): 49–56.
- Wang X, Hu H, Wang Q, et al. The calibration method of soil model parameters based on discrete element (Chinese). Transactions of the Chinese Society for Agricultural Machinery 2017; 48(12): 78–85.
Supporting Agencies
Copyright (c) 2022 Lipengcheng Wan, Yonglei Li, Hu Zhao, Guanghao Xu, Jiannong Song, Xiangqian Dong, Chao Zhang, Jicheng Wang

This work is licensed under a Creative Commons Attribution 4.0 International License.
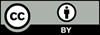
This site is licensed under a Creative Commons Attribution 4.0 International License (CC BY 4.0).
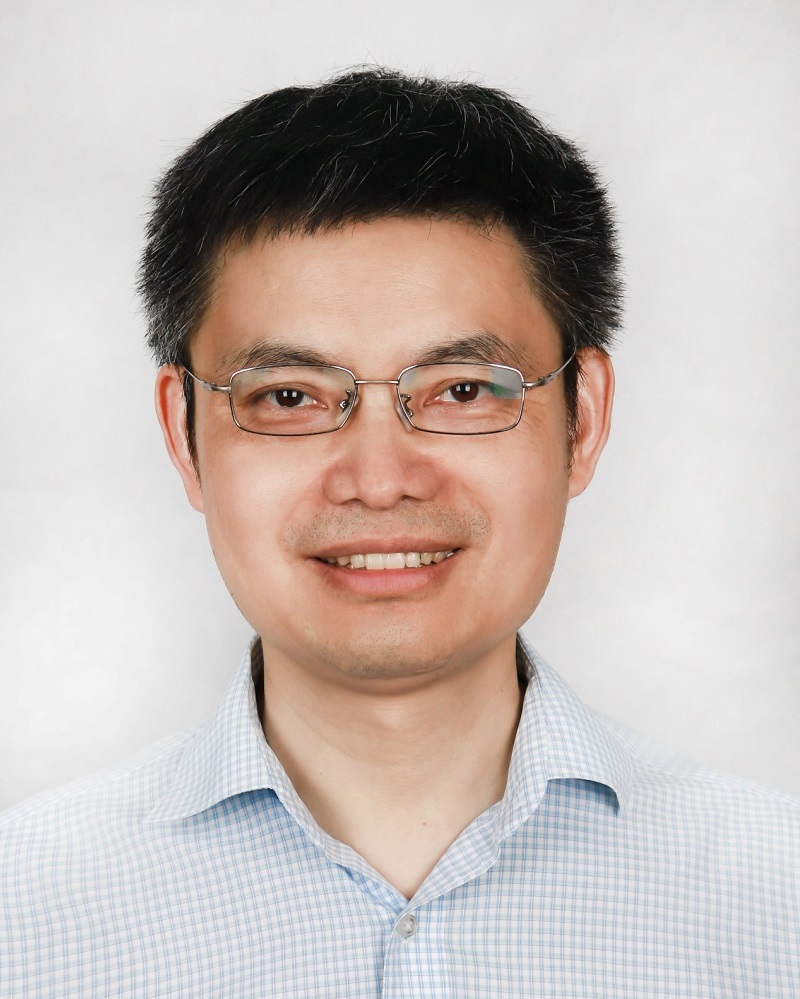
Prof. Zhengjun Qiu
Zhejiang University, China
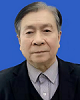
Cheng Sun
Academician of World Academy of Productivity Science; Executive Chairman, World Confederation of Productivity Science China Chapter, China
Indexing & Archiving
In the realm of modern agriculture, the integration of cutting-edge technologies is revolutionizing the way we approach sustainable farming practices. A recent study published in Advances in Modern Agriculture titled "Classification of cotton water stress using convolutional neural networks and UAV-based RGB imagery" has garnered significant attention for its innovative approach to precision irrigation management. Conducted by researchers from Institute of Data Science and the AgriLife Research and Extension Center of Texas A&M University (authors's information is below). This study introduces a novel method for classifying cotton water stress using unmanned aerial vehicles (UAVs) and convolutional neural networks (CNNs), offering a powerful solution for optimizing water use in agriculture.
Modern agricultural technology is evolving rapidly, with scientists collaborating with leading agricultural enterprises to develop intelligent management practices. These practices utilize advanced systems that provide tailored fertilization and treatment options for large-scale land management.
This journal values human initiative and intelligence, and the employment of AI technologies to write papers that replace the human mind is expressly prohibited. When there is a suspicious submission that uses AI tools to quickly piece together and generate research results, the editorial board of the journal will reject the article, and all journals under the publisher's umbrella will prohibit all authors from submitting their articles.
Readers and authors are asked to exercise caution and strictly adhere to the journal's policy regarding the usage of Artificial Intelligence Generated Content (AIGC) tools.
Asia Pacific Academy of Science Pte. Ltd. (APACSCI) specializes in international journal publishing. APACSCI adopts the open access publishing model and provides an important communication bridge for academic groups whose interest fields include engineering, technology, medicine, computer, mathematics, agriculture and forestry, and environment.