
Asia Pacific Academy of Science Pte. Ltd. (APACSCI) specializes in international journal publishing. APACSCI adopts the open access publishing model and provides an important communication bridge for academic groups whose interest fields include engineering, technology, medicine, computer, mathematics, agriculture and forestry, and environment.
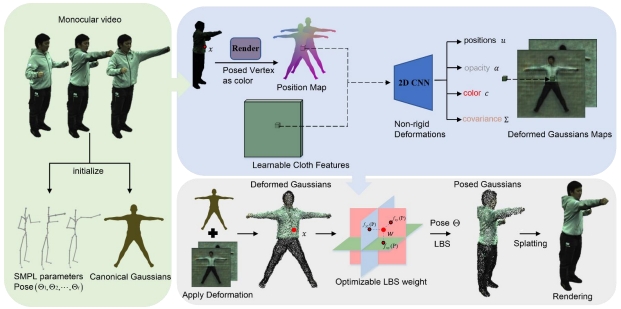
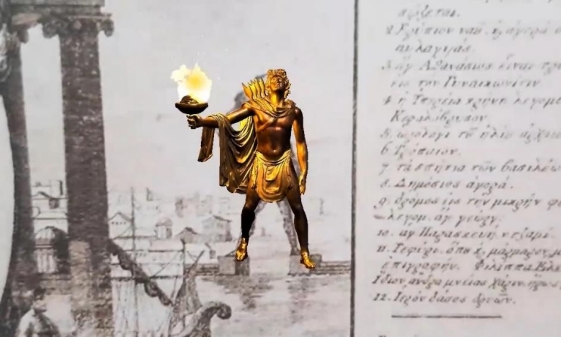
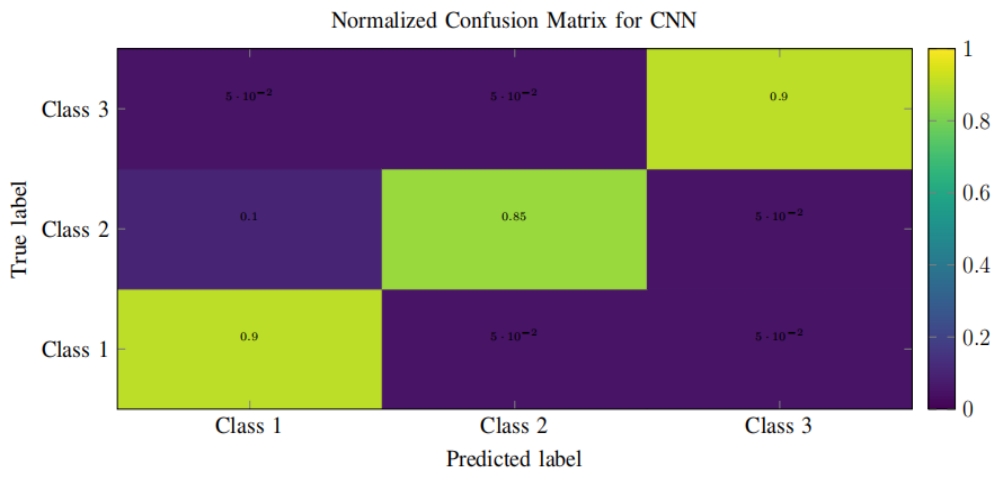
Artificial intelligence and machine learning for additive manufacturing composites toward enriching Metaverse technology
Vol 5, Issue 2, 2024
Download PDF
Abstract
As a result of the growing significance and application of technology across a wide range of fields, digital environments such as Metaverse started to take shape over the span of the previous decade. This study aims to discover an area of engineering that could benefit from this new technology by developing an artificial intelligence (AI)—based approach to analyzing and predicting the mechanical properties of carbon fiber reinforced syntactic thermoset composites that are made through additive manufacturing (AM). These composites are intended to be utilized as a tool for metaverse technology in a variety of domains—as the presence of the limitations in the currently experimental methods. The metaverse allows for the generation of simulations through the application of artificial intelligence (AI) and machine learning (ML). Consequently, this paves the way for individuals to investigate various design possibilities and view the virtual manifestation of those possibilities. This is made possible by the use of machine learning algorithms, which allow for the monitoring and evaluation of user performance, as well as the provision of individualized feedback and suggestions for improvement. As a consequence of this, it is feasible that professionals will be able to get education and training that are both more efficient and effective. Consequently, this work aims to introduce an Adaptive Neuro-Fuzzy Inference System (ANFIS)—based model, which is able to effectively anticipate the behavior of mechanical systems in a variety of settings without the need for significant measurements. The validity of the ANFIS model was determined through the utilization of flexure and compression testing. The approach that was used to improve the technical assessment of the manufactured composites—is verified by the model’s near-realistic predictions. Moreover, this method is superb for lowering weight, enhancing mechanical qualities, and minimizing product complexity.
Keywords
References
- Zhao R, Zhang Y, Zhu Y, et al. Metaverse: Security and Privacy Concerns. Journal of Metaverse. 2023; 3(2): 93-99. doi: 10.57019/jmv.1286526
- Lee LH, Braud T, Zhou P, et al. All one needs to know about metaverse: A complete survey on technological singularity, virtual ecosystem, and research agenda. arXiv. 2021; arXiv:2110.05352.
- Falchuk B, Loeb S, Neff R. The Social Metaverse: Battle for Privacy. IEEE Technology and Society Magazine. 2018; 37(2): 52-61. doi: 10.1109/mts.2018.2826060
- Far SB, Rad AI. Applying digital twins in metaverse: User interface, security and privacy challenges. Journal of Metaverse. 2022; 2(1): 8-15.
- Duan H, Li J, Fan S, et al. Metaverse for Social Good. Proceedings of the 29th ACM International Conference on Multimedia. Published online October 17, 2021. doi: 10.1145/3474085.3479238
- Huynh-The T, Pham QV, Pham XQ, et al. Artificial intelligence for the metaverse: A survey. Engineering Applications of Artificial Intelligence. 2023; 117: 105581. doi: 10.1016/j.engappai.2022.105581
- Kumar D, Haque A, Mishra K, et al. Exploring the Transformative Role of Artificial Intelligence and Metaverse in Education: A Comprehensive Review. Metaverse Basic and Applied Research. 2023; 2: 55. doi: 10.56294/mr202355
- Bibri SE, Jagatheesaperumal SK. Harnessing the Potential of the Metaverse and Artificial Intelligence for the Internet of City Things: Cost-Effective XReality and Synergistic AIoT Technologies. Smart Cities. 2023; 6(5): 2397-2429. doi: 10.3390/smartcities6050109
- Huynh-The T, Gadekallu TR, Wang W, et al. Blockchain for the metaverse: A Review. Future Generation Computer Systems. 2023; 143: 401-419. doi: 10.1016/j.future.2023.02.008
- Villegas-Ch W, García-Ortiz J, Sánchez-Viteri S. Educational Advances in the Metaverse: Boosting Learning Through Virtual and Augmented Reality and Artificial Intelligence. IEEE Access. 2024; 12: 59093-59112. doi: 10.1109/access.2024.3393776
- Mah E. Metaverse, AR, machine learning & AI in Orthopaedics? Journal of Orthopaedic Surgery. 2023; 31(1): 102255362311653. doi: 10.1177/10225536231165362
- Hayajneh M, AL-Oqla FM, Aldhirat A. Physical and Mechanical Inherent Characteristic Investigations of Various Jordanian Natural Fiber Species to Reveal Their Potential for Green Biomaterials. Journal of Natural Fibers. 2021; 19(13): 7199-7212. doi: 10.1080/15440478.2021.1944432
- Ismail AHM, AL-Oqla FM, Risby MS, et al. On the enhancement of the fatigue fracture performance of polymer matrix composites by reinforcement with carbon nanotubes: a systematic review. Carbon Letters. 2022; 32(3): 727-740. doi: 10.1007/s42823-022-00323-z
- AL-Oqla FM, Al-Jarrah R. A novel adaptive neuro-fuzzy inference system model to predict the intrinsic mechanical properties of various cellulosic fibers for better green composites. Cellulose. 2021; 28(13): 8541-8552. doi: 10.1007/s10570-021-04077-1
- Gupta N, Zeltmann SE, Shunmugasamy VC, et al. Applications of Polymer Matrix Syntactic Foams. JOM. 2013; 66(2): 245-254. doi: 10.1007/s11837-013-0796-8
- Wouterson EM, Boey FYC, Hu X, et al. Specific properties and fracture toughness of syntactic foam: Effect of foam microstructures. Composites Science and Technology. 2005; 65(11-12): 1840-1850. doi: 10.1016/j.compscitech.2005.03.012
- Gupta N, Nagorny R. Tensile properties of glass microballoon‐epoxy resin syntactic foams. Journal of Applied Polymer Science. 2006; 102(2): 1254-1261. doi: 10.1002/app.23548
- Walter TR, Sietins J, Moy P. Evaluation of Syntactic Foam for Energy Absorption at Low to Moderate Loading Rates. Advanced Composites for Aerospace, Marine, and Land Applications II. Published online January 16, 2015: 233-244. doi: 10.1002/9781119093213.ch18
- Patil B, Bharath Kumar BR, Doddamani M. Compressive behavior of fly ash based 3D printed syntactic foam composite. Materials Letters. 2019; 254: 246-249. doi: 10.1016/j.matlet.2019.07.080
- Peroni L, Scapin M, Fichera C, et al. Investigation of the mechanical behaviour of AISI 316L stainless steel syntactic foams at different strain-rates. Composites Part B: Engineering. 2014; 66: 430-442. doi: 10.1016/j.compositesb.2014.06.001
- Singh AK, Patil B, Hoffmann N, et al. Additive Manufacturing of Syntactic Foams: Part 1: Development, Properties, and Recycling Potential of Filaments. JOM. 2018; 70(3): 303-309. doi: 10.1007/s11837-017-2734-7
- Zamani P, FM da Silva L, Masoudi Nejad R, et al. Experimental study on mixing ratio effect of hybrid graphene nanoplatelet/nano-silica reinforcement on the static and fatigue life of aluminum-to-GFRP bonded joints under four-point bending. Composite Structures. 2022; 300: 116108. doi: 10.1016/j.compstruct.2022.116108
- NajiMehr H, Shariati M, Zamani P, et al. Investigating on the influence of multi‐walled carbon nanotube and graphene nanoplatelet additives on residual strength of bonded joints subjected to partial fatigue loading. Journal of Applied Polymer Science. 2021; 139(18). doi: 10.1002/app.52069
- Zhong W, Li F, Zhang Z, et al. Short fiber reinforced composites for fused deposition modeling. Materials Science and Engineering. 2001; 301(2): 125-130.
- Huang T, Wang S, He K. Quality control for fused deposition modeling based additive manufacturing: Current research and future trends. 2015 First International Conference on Reliability Systems Engineering (ICRSE). Published online October 2015. doi: 10.1109/icrse.2015.7366500
- Takagi T, Sugeno M. Fuzzy identification of systems and its applications to modeling and control. IEEE Transactions on Systems, Man, and Cybernetics. 1985; SMC-15(1): 116-132. doi: 10.1109/tsmc.1985.6313399
Supporting Agencies
Copyright (c) 2024 Faris M. AL-Oqla, Nashat Nawafleh
License URL: https://creativecommons.org/licenses/by/4.0/
This site is licensed under a Creative Commons Attribution 4.0 International License (CC BY 4.0).
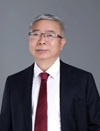
Prof. Zhigeng Pan
Director, Institute for Metaverse, Nanjing University of Information Science & Technology, China
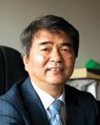
Prof. Jianrong Tan
Academician, Chinese Academy of Engineering, China
Conference Time
December 15-18, 2025
Conference Venue
Hong Kong Convention and Exhibition Center (HKCEC)
...
Metaverse Scientist Forum No.3 was successfully held on April 22, 2025, from 19:00 to 20:30 (Beijing Time)...
We received the Scopus notification on April 19th, confirming that the journal has been successfully indexed by Scopus...
We are pleased to announce that we have updated the requirements for manuscript figures in the submission guidelines. Manuscripts submitted after April 15, 2025 are required to strictly adhere to the change. These updates are aimed at ensuring the highest quality of visual content in our publications and enhancing the overall readability and impact of your research. For more details, please find it in sumissions...